Automotive parts manufacturer enhances product quality and customer trust with BarTender
BarTender streamlines labeling operations and ensures regulatory compliance following rapid deployment
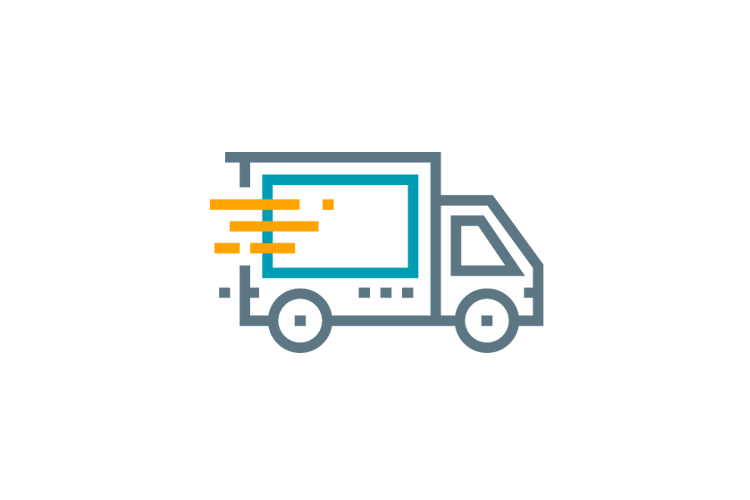
“BarTender was easy to understand, quick to learn, and easy to change when needed. Their simple processes made it easy to train floor personnel and their support staff were quick to resolve issues and always pleasant. They fixed anything I could throw at them. It’s a very solid platform.”
- Leo Haas, Technology Consultant
critical challenges:
-
Inadequate label management led to high costs to identify products
-
Manual processes and errors led to relabeling and resource waste
-
Regulatory risks and financial consequences when label compliance was not met
bartender benefits:
-
Efficient implementation and training led to boosts in worker productivity
-
Streamlined label production allowed for easy label creation for new and existing products
-
Dynamic label customization saved time required for processing new labels
Ready to get started?
Founded in 2003, this company is a prominent aftermarket auto parts supplier, known for its commitment to rugged durability and innovative product refinement. Specializing in the design, manufacturing, and distribution of high-quality aftermarket accessories and products for trucks and SUVs, the company has established itself as a trusted brand through advanced manufacturing processes, top-grade materials, and superior strength and longevity. The brand is renowned among truck and SUV enthusiasts, and the off-roading community.
Challenge: Regulatory Compliance Leads to Manual Label Processing—and Rocketing Labor Costs
Labelling not only plays a crucial role in providing proper product identification and branding for this company—it’s essential to maintaining regulatory compliance, traceability, quality assurance, counterfeit prevention, and inventory management.
Without a reliable label management solution, the company’s operations and sales were vulnerable to financial fallout and poor customer experience. Improper product identification could create issues throughout the entire supply chain, which was previously addressed by manually noting and referencing each individual product’s information. However, manual validation and processing proved to be time-consuming and required a large amount of human resources and coordination, while introducing multiple points for potential errors.
In addition to the high costs of manually sorting and identifying products, aftermarket automotive manufacturers must comply with various regulations and standards set by the National Highway Traffic Safety Administration (NHTSA) based on safety needs. Different states hold different vehicle safety laws—making accurate and complete information on aftermarket automotive products essential. It is the manufacturer’s responsibility to meet these compliance requirements and failing to do so can result in serious fines.
Solution: Fast Deployment, Easy Integration, Time-saving Automations
The company was able to onboard BarTender and train staff within days. Guided label template workflows allowed the team to quickly build industry-compliant labels, redirecting the team’s time towards customer order processing and shipping. The company produced hundreds of thousands of labels every year for various parts, products, and shipping containers. Considering this volume, accurate and efficient label processing is a critical success factor for their operations. Each label serves a very specific purpose, from providing product-related information internally, to getting key attributes into the hands of stakeholders and end customers.
To enhance label accuracy, the team integrated BarTender Automation Edition with Quickbooks, and used its database as their source of truth for label information. This allowed BarTender to print labels on-demand with dynamic customized information, saving labeling operators time spent editing label details such as date, time, customer information, product specifications, and serialization.
In addition to processing orders, labels were used to prominently display the company’s brand. Product labels provided information about origin, quality, and specifications, but also provided customers with brand assurance. Enhanced branding and labeling information helped to build trust and recognition among consumers, contributing to overall business success.